Awe-Inspiring Examples Of Tips About What Is A BOM In Purchase Order
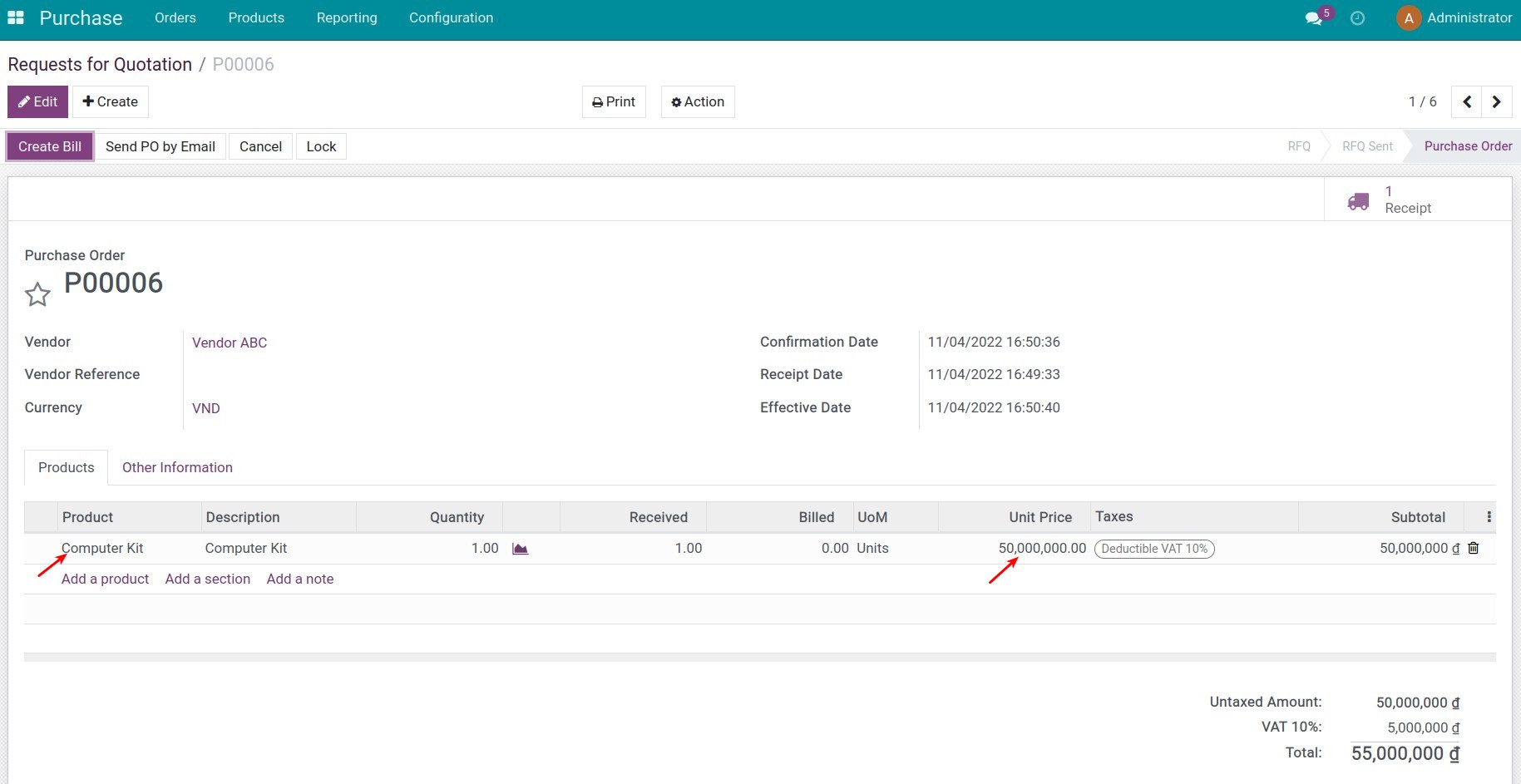
Purchase BoM Stock Value For Odoo 15.0
Demystifying the BOM in Your Purchase Order
1. What exactly is a BOM?
Alright, let's cut to the chase. You've probably seen "BOM" lurking on a purchase order and maybe even scratched your head wondering what it signifies. Rest assured, it's not some kind of explosive device about to detonate your budget. BOM stands for "Bill of Materials." Think of it as an ingredient list, but instead of flour and sugar, it's all the parts and pieces needed to make something bigger. We're talking about the nuts, bolts, widgets, and thingamajigs that go into creating a finished product.
Consider a simple example: a chair. The BOM for that chair would list everything required to build it. That includes the wooden legs, the seat cushion, screws, glue, and any fabric used for upholstery. Each item on the BOM should have a specified quantity, allowing the purchaser (you!) to accurately determine the total cost and ensure you order enough of everything. The more complex the product, the more extensive (and potentially headache-inducing!) the BOM.
The Bill of Materials (BOM) in a purchase order is the keyword term we use to this article. The term is a noun, and understanding its role is vital for streamlining procurement. It's the blueprint, the shopping list, the secret sauce — okay, maybe not secret sauce, but definitely important!
Without a well-defined BOM, chaos can quickly ensue. Picture this: you order a bunch of chair legs but forget the screws. Now you're stuck with a pile of useless legs and an angry customer who wants somewhere to sit! A complete and accurate BOM prevents these sorts of costly mistakes, ensures efficient production, and helps you keep your sanity intact. It's basically the difference between a smooth-sailing manufacturing process and a logistical nightmare.
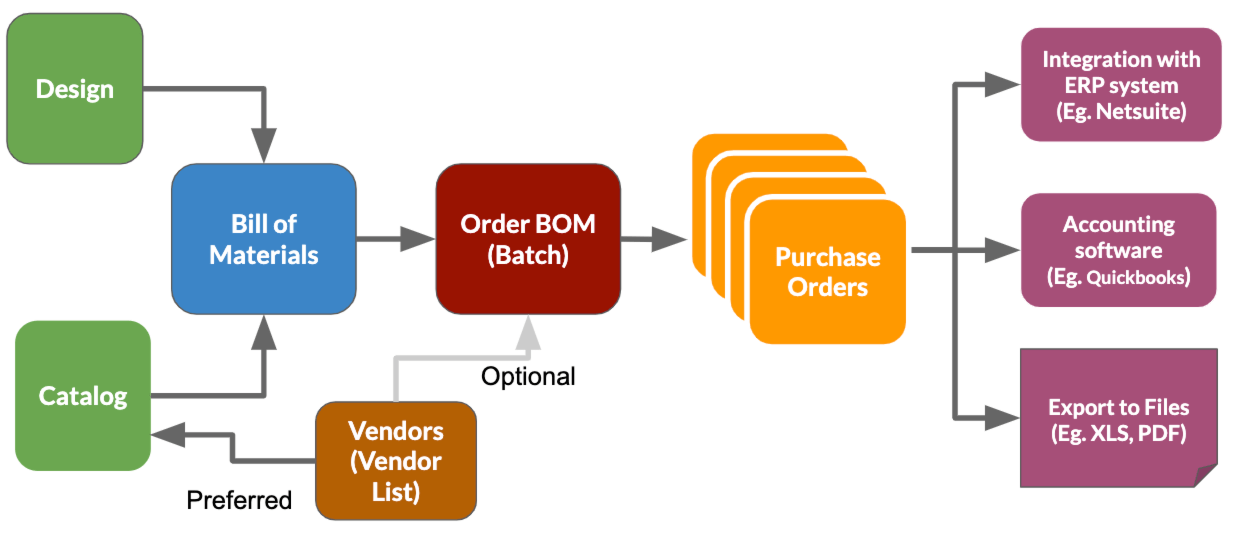
Bill Of Materials For AIDriven Product Development Decisions OpenBOM
Why is the BOM So Darn Important Anyway?
2. The Ripple Effects of a Good BOM
Okay, so we know a BOM is a list of stuff. But why should you care? Well, a well-structured BOM is the backbone of efficient manufacturing and supply chain management. Its more than just a shopping list; it's a critical communication tool between different departments and even different companies. From engineering and purchasing to manufacturing and accounting, everyone relies on the BOM for accurate information.
Imagine the engineering team designing a new gadget. Their initial design informs the BOM. Purchasing then uses the BOM to source the necessary components. Manufacturing follows the BOM to assemble the product correctly. And accounting uses the BOM to track costs and calculate profit margins. It's a beautiful, interdependent system (when it works!). The BOM acts as the single source of truth, ensuring everyone is on the same page.
A precise BOM minimizes errors in ordering. It avoids the expensive scenario where you over- or under-order components. This is helpful in budget planning, especially when you are dealing with small business operations. An adequate BOM ensures that businesses maintain optimal inventory levels. This in turn reduces the associated costs of storing excessive inventory or the dangers of production halts because of a lack of necessary parts.
Here's another way to think about it: consider it as a recipe that leads to the perfect product. You wouldn't want to bake a cake with half the ingredients, would you? The same logic applies here. A complete BOM results in a great final outcome!

Planning BOMs And Purchase Orders OpenBOM Training Library
Types of BOMs
3. Not all BOMs are created equal!
Just like there are different types of sandwiches (who doesn't love a good sandwich analogy?), there are different types of BOMs. Knowing the nuances of each can help you choose the right one for your specific needs.
One common type is the Manufacturing BOM (MBOM). This focuses on all the parts and assemblies needed to manufacture a finished product, including raw materials, sub-assemblies, and packaging. It's the go-to BOM for the manufacturing floor.
Then there's the Engineering BOM (EBOM). This is created during the product design phase and lists all the parts and components as designed by the engineering team. It's often more conceptual and may not reflect the actual manufacturing process perfectly.
Finally, there's the Sales BOM (SBOM). This is used to define products sold as a package or kit. Think of a computer bundle that includes a monitor, keyboard, and mouse. The SBOM would list each of these items as part of the complete sales offering. Choosing the correct BOM allows you to fine-tune your entire operations strategy.
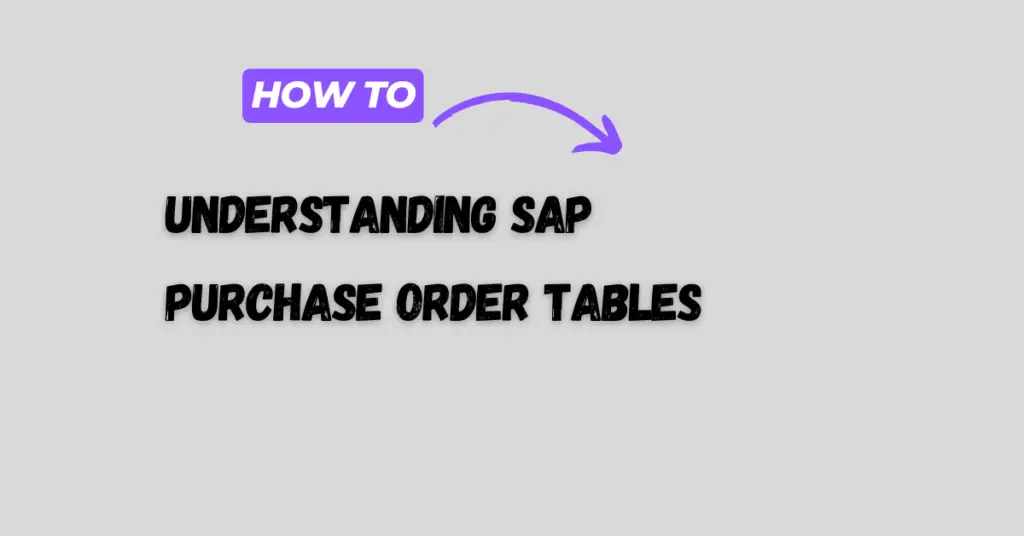
BOM Table In SAP Understanding Its Role And Functionality Tables
Beyond the List
4. Getting the Most Out of Your BOM
Creating a BOM isn't just about listing parts; it's about doing it right. Following best practices can significantly improve efficiency and reduce errors.
First, ensure your BOM is accurate and up-to-date. Regularly review and update it to reflect any changes in design, materials, or manufacturing processes. Outdated BOMs can lead to costly mistakes and production delays.
Second, use a clear and consistent format. Standardize your naming conventions and include relevant information such as part numbers, descriptions, quantities, and units of measure. Consistency makes it easier for everyone to understand and use the BOM.
Third, consider using BOM management software. These tools can automate many of the tasks involved in creating and maintaining BOMs, reducing manual effort and improving accuracy. They can also integrate with other business systems, such as ERP and CRM.
Finally, involve all stakeholders in the BOM creation process. Get input from engineering, purchasing, manufacturing, and other relevant departments to ensure the BOM reflects the needs of everyone involved. Collaboration is key to a successful BOM.
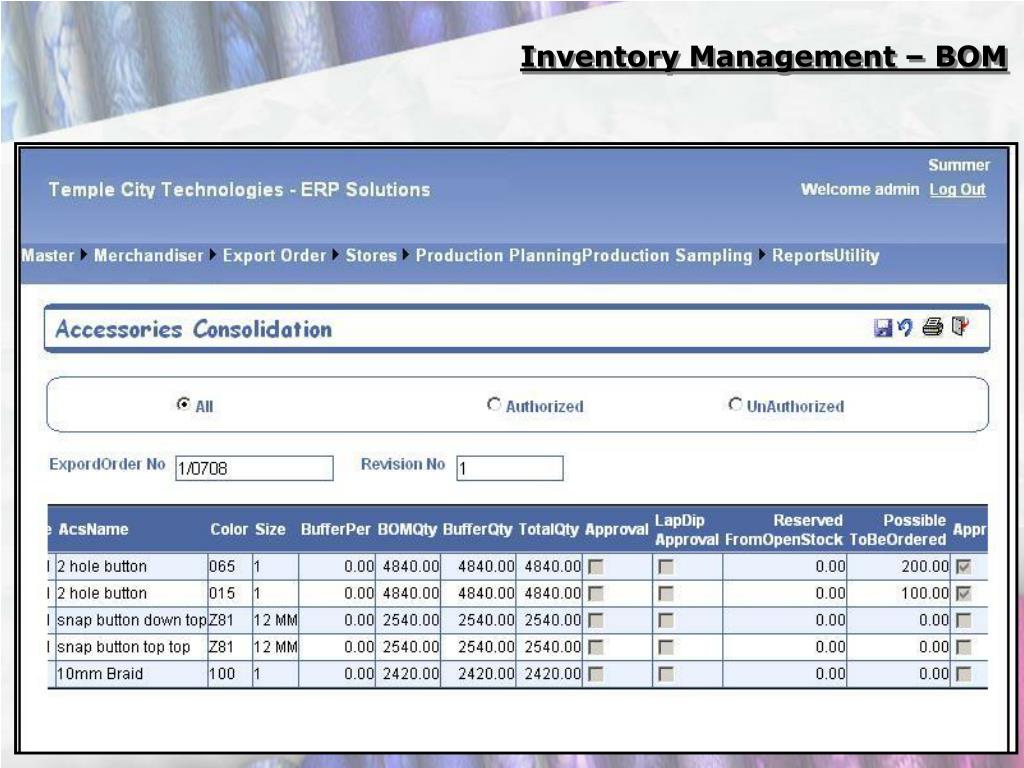
PPT A Friendly ERP Solution For Apparel Industry PowerPoint
Frequently Asked Questions (FAQs)
5. Your BOM Questions Answered
Still have questions about BOMs? Here are some common queries to help clear things up:
Q: What's the difference between a BOM and a parts list?
A: While similar, a BOM is more comprehensive than a simple parts list. A BOM includes not just the parts but also their quantities, descriptions, and hierarchical relationships (how they fit together).
Q: How often should I update my BOM?
A: As often as needed! Any time there's a change in design, materials, or manufacturing, the BOM should be updated to reflect that change. Regularly reviewing the BOM is also a good practice.
Q: Can I use a spreadsheet to manage my BOM?
A: For very simple products, a spreadsheet might suffice. However, for more complex products or businesses, BOM management software is highly recommended to improve accuracy and efficiency.
Q: What are the key elements to include in a BOM?
A: A BOM should include Part Number, Part Name/Description, Quantity, Unit of Measure, Procurement Type (make or buy), and any relevant notes or comments.
