Looking Good Info About How To Create A Bill Of Materials
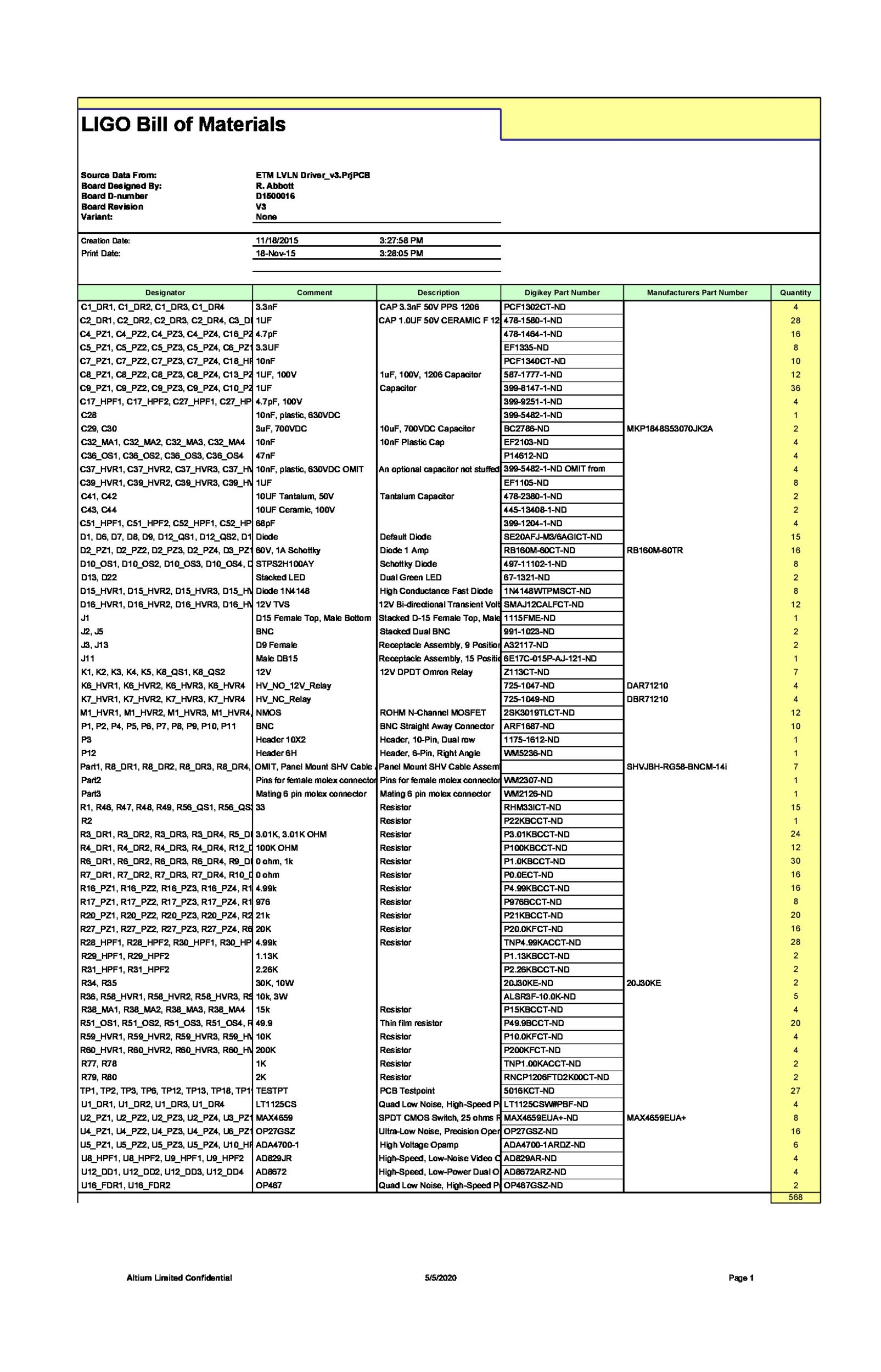
Build Of Materials Excel Template
Unlocking the Secrets of a Bill of Materials
1. What in the World is a Bill of Materials, Anyway?
Okay, let's say you're building something amazing, like a super-powered robot vacuum cleaner or a birdhouse that attracts only the coolest birds. You wouldn't just start throwing random parts together, right? You'd need a list. A list that tells you exactly what you need, how much of it you need, and where to find it. That list, my friend, is a Bill of Materials, or BOM for short. Think of it as the recipe for your masterpiece. Without it, you're basically just winging it, and that rarely ends well (especially when robotics are involved).
A Bill of Materials (BOM) is a comprehensive list of all the raw materials, components, assemblies, sub-assemblies, parts, and quantities needed to manufacture an end product. It's like the ultimate shopping list for your project, ensuring you have everything you need to create your final product efficiently and accurately. Whether you're making a single item or mass-producing thousands, a well-crafted BOM is absolutely essential.
Think of it this way: if you're baking a cake, your BOM is your recipe card. It tells you exactly how much flour, sugar, eggs, and other ingredients you'll need. Without it, you might end up with a cake that's either too sweet, too dry, or just plain weird. Similarly, a BOM ensures that your product is built correctly, with the right components, in the right quantities. This minimizes errors, reduces waste, and ultimately saves you time and money. It's kind of like having a personal assistant who keeps track of all the little details, so you can focus on the big picture. And who wouldn't want that?
So, why is this "Bill of Materials" thing so important? Well, it's the backbone of efficient manufacturing. It helps with inventory management, ensures accurate costing, aids in production planning, and even assists in regulatory compliance. In short, it's the secret sauce that keeps everything running smoothly from design to delivery. Imagine trying to build a car without knowing how many tires you need. Chaos, right? That's why understanding how to create a bill of materials is crucial for anyone involved in product development and manufacturing. Trust me, your future self will thank you for it.
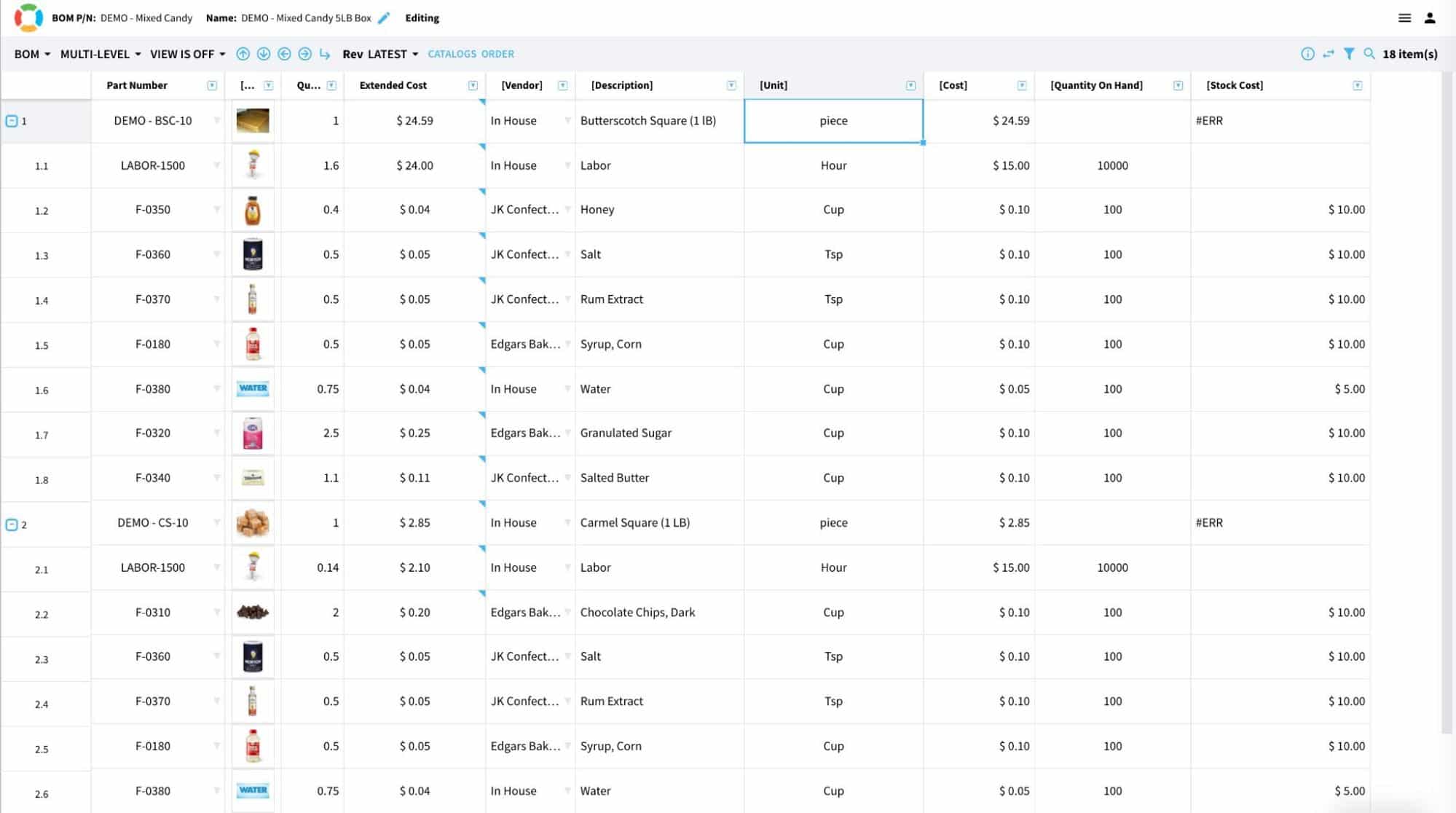
How To Create A Bill Of Materials OpenBOM
Getting Down to Business
2. Step 1
First things first, let's be crystal clear about what you're actually building. What's the finished product? What are all the different parts and sub-assemblies that go into it? Think of it like dissecting a frog in biology class (hopefully a virtual one!). You need to break down the entire product into its smallest, most manageable pieces. This is where good documentation and clear design specifications become your best friends. The more detailed you are, the easier the rest of the process will be. Imagine trying to assemble IKEA furniture without the instructions — that's what it's like building a product without a well-defined BOM. Painful!
Start by creating a top-level assembly. This is your final product. Then, start breaking it down into its sub-assemblies and individual components. For each component, note its name, description, and any relevant specifications. This might include dimensions, materials, or even the specific manufacturer and part number. The more information you capture upfront, the less likely you are to encounter problems later on. It's like packing for a trip — the more you plan ahead, the less likely you are to forget something important (like your toothbrush!).
Don't underestimate the power of visual aids. Diagrams, drawings, and even 3D models can be incredibly helpful in visualizing the product and its components. They can also make it easier to communicate your design to others. Consider using CAD software or even just a simple sketch to illustrate how everything fits together. Remember, a picture is worth a thousand words, especially when you're trying to explain a complex assembly to someone who's never seen it before. It's like showing someone a map instead of just giving them directions — much easier to follow!
Finally, remember to be thorough. It's better to over-document than under-document. If you're not sure whether a particular component should be included in the BOM, err on the side of caution and add it. You can always remove it later if necessary. But forgetting a crucial part can lead to delays, errors, and a whole lot of frustration. Think of it like double-checking your work before submitting it — it might seem tedious, but it can save you from making a silly mistake. And nobody wants a silly mistake ruining their masterpiece!
3. Step 2
Now that you've identified all the parts, it's time to organize them. Think of it like organizing your closet. You wouldn't just throw everything in there haphazardly, would you? You'd want to group similar items together, like shirts with shirts and pants with pants. The same goes for your BOM. You need to create a structure that makes sense and allows you to easily find what you're looking for.
There are several different ways to structure a BOM, but the most common is a hierarchical structure. This means that the BOM is organized in a tree-like fashion, with the top-level assembly at the root and the sub-assemblies and components branching out from there. This makes it easy to see how everything fits together and to navigate the BOM quickly. Think of it like a family tree — you can easily see how everyone is related to each other.
Another important aspect of the BOM structure is defining the level of detail. How far down do you want to break down the components? Do you want to include every nut and bolt, or just the major sub-assemblies? The answer to this question depends on your specific needs and the complexity of your product. In general, it's better to be more detailed than less detailed. But you also need to balance that with the amount of time and effort required to create and maintain the BOM. It's like deciding how much detail to include in a map — you want enough information to be useful, but not so much that it becomes overwhelming.
Consider using a numbering system to identify each component in the BOM. This can make it easier to track components and to refer to them in other documents. There are several different numbering systems you can use, but the most important thing is to be consistent. Choose a system and stick with it. It's like choosing a file naming convention — consistency is key to keeping everything organized and easy to find. And nobody wants to spend hours searching for a file because it's named something cryptic like "document1.docx."
4. Step 3
Alright, you've got your structure, now it's time to fill it in! This is where you actually enter all the data for each component. We're talking part numbers, descriptions, quantities, materials, costs — the whole shebang. Think of it like filling out a tax form. You need to be accurate and thorough, because even a small mistake can cause big problems later on. No one wants to deal with a tax audit, and nobody wants to deal with a BOM that's full of errors!
For each component, you'll want to include a unique part number. This is a unique identifier that distinguishes the component from all other components in the BOM. The part number should be consistent and easy to understand. You might also want to include the manufacturer's part number, if applicable. This can be helpful for ordering components and for tracking them throughout the supply chain. It's like having a social security number for each component — it's unique and helps to identify it.
The description should be clear and concise. It should accurately describe the component and its function. Avoid using jargon or technical terms that might not be understood by everyone who uses the BOM. You might also want to include a link to a datasheet or other relevant documentation. The quantity is the number of units of the component required for each unit of the final product. Be sure to specify the units of measure (e.g., pieces, feet, meters). It's like specifying the units when you're baking a cake — you need to know whether you're talking about cups, tablespoons, or teaspoons.
Don't forget the materials! Specifying the materials used to manufacture the component is crucial for costing and for ensuring that the component meets the required performance specifications. You might also want to include the supplier of the component. This can be helpful for ordering components and for negotiating prices. It's like knowing where to buy the best ingredients for your cake — you want to get the best quality at the best price. Adding cost information, even estimated, is highly recommended for budgeting and profit margin calculations.
5. Step 4
Let's face it, managing a BOM with just a spreadsheet can quickly become a nightmare, especially for complex products. There are dedicated BOM software tools out there that can make your life a whole lot easier. Think of it like upgrading from a manual typewriter to a computer — it's a game changer! These tools can help you organize your data, track changes, generate reports, and even integrate with other systems like ERP and MRP. They also often have built-in version control, ensuring you're always working with the latest and greatest BOM. Trust me, your sanity is worth the investment.
When choosing a BOM software, consider factors like your budget, the complexity of your products, and the number of users who will need access. Some software is designed for small businesses with simple products, while others are designed for large enterprises with complex supply chains. There are also open-source options available, which can be a good choice if you're on a tight budget. It's like choosing a car — you need to find one that fits your needs and your budget. A tiny sports car isn't much use if you have 5 kids.
If you're not ready to invest in dedicated BOM software, you can still use a spreadsheet. Just be sure to use it carefully and to implement some basic version control practices. Create a template with all the necessary columns, and use formulas to automate calculations. You can also use features like data validation to prevent errors. But be warned, spreadsheets can become unwieldy very quickly. So, if you're planning on building complex products, it's worth considering a dedicated BOM software solution. Think of it like using a paper map versus using GPS. Both will get you there, but one is way more efficient and less likely to lead you astray.
No matter which tool you choose, it's important to train your team on how to use it effectively. This will help to ensure that everyone is using the same data and that the BOM is accurate and up-to-date. Provide clear instructions and guidelines, and be available to answer questions. Remember, even the best software is useless if nobody knows how to use it properly. It's like buying a fancy new camera but never learning how to take pictures with it. You'll just end up with blurry photos of your cat.
6. Step 5
Creating a BOM isn't a one-and-done thing. Products change, designs evolve, suppliers go out of business (hopefully not yours!). Your BOM needs to keep up. Think of it like your social media profile — you need to keep it updated with your latest information and activities. An outdated BOM is about as useful as a dinosaur in the 21st century. Regularly review and update your BOM to reflect any changes in your product, its components, or your suppliers. This includes adding new components, removing obsolete components, and updating quantities and prices. This is not optional!
Implement a formal change management process to ensure that all changes to the BOM are properly documented and approved. This process should include a review of the proposed changes, an assessment of their impact on the product, and an approval from the relevant stakeholders. This will help to prevent errors and to ensure that the BOM remains accurate and consistent. It's like having a quality control process in a factory — it helps to catch defects before they become a problem.
Consider using version control to track changes to the BOM over time. This will allow you to easily revert to previous versions if necessary and to see who made which changes. Version control is especially important if you have multiple users who are working on the BOM. It's like having a backup copy of your computer files — it can save you a lot of heartache if something goes wrong.
Finally, regularly audit your BOM to ensure that it is accurate and complete. This should include a review of the BOM against the actual product and a verification of the component quantities and prices. An audit can help to identify errors and to ensure that the BOM is in sync with your inventory and your production processes. It's like having a physical inventory count in a warehouse — it helps to ensure that your records match reality.

Excel Bill Of Materials Template
FAQ
7. Q
A: Think of a single-level BOM as a simple grocery list — just the ingredients for the final product. A multi-level BOM, on the other hand, is like a recipe with sub-recipes. It breaks down the components into sub-assemblies, then lists the parts that make up each sub-assembly. Multi-level BOMs are essential for complex products.
8. Q
A: As often as your product changes! Seriously, any time there's a design change, a new component, or a supplier switch, your BOM needs an update. The more frequently you update it, the less likely you are to run into problems down the road. Consider implementing a formal change management process to ensure that all changes are properly documented and approved. It's like brushing your teeth — you need to do it regularly to prevent cavities (or, in this case, costly errors).
9. Q
A: Absolutely! A service BOM lists the parts needed for repairs or maintenance. This is incredibly useful for field technicians and service departments. It ensures they have the right parts on hand to get the job done quickly and efficiently. It's like having a toolbox with all the right tools — you're prepared for anything!

HowTo Series Create Bill Of Materials YouTube
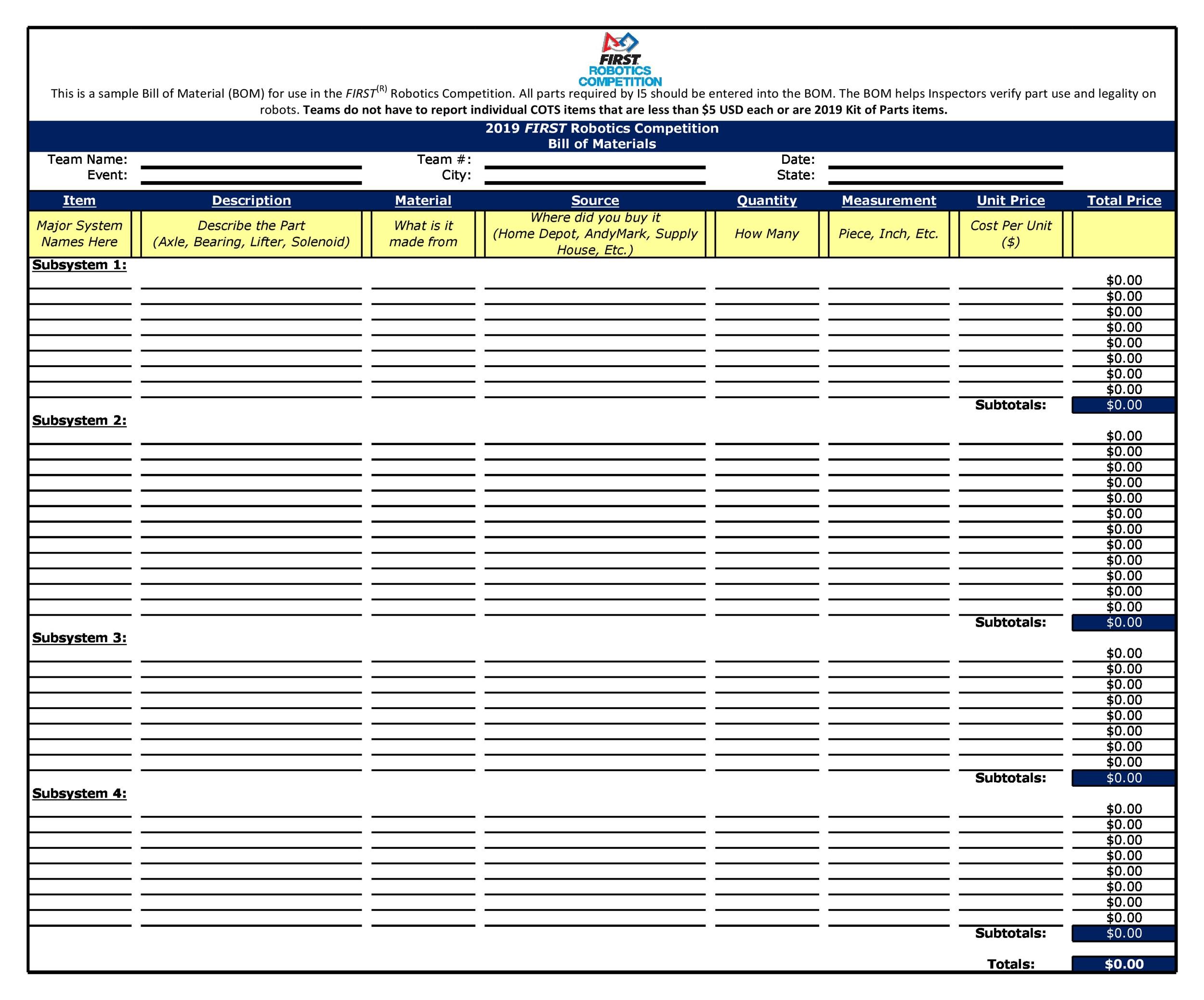
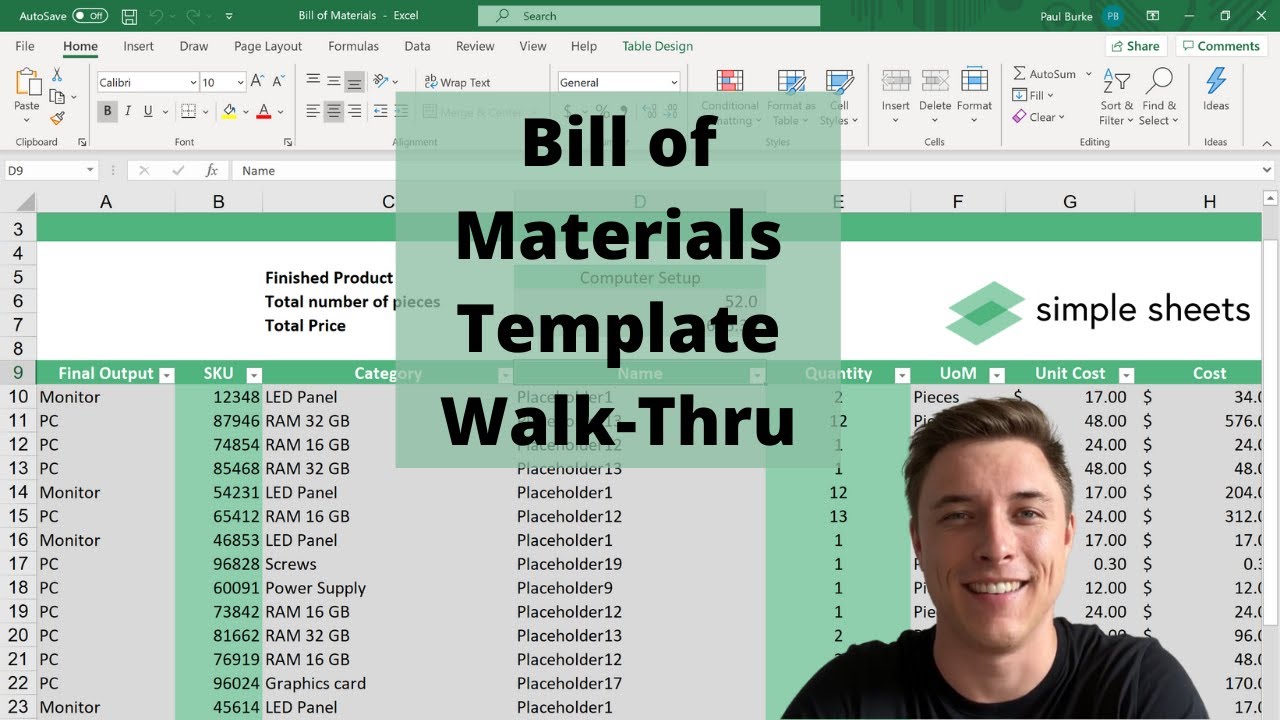